Discover the Benefits of Patio Screen Mesh for Outdoor Comfort and Style
By:Admin
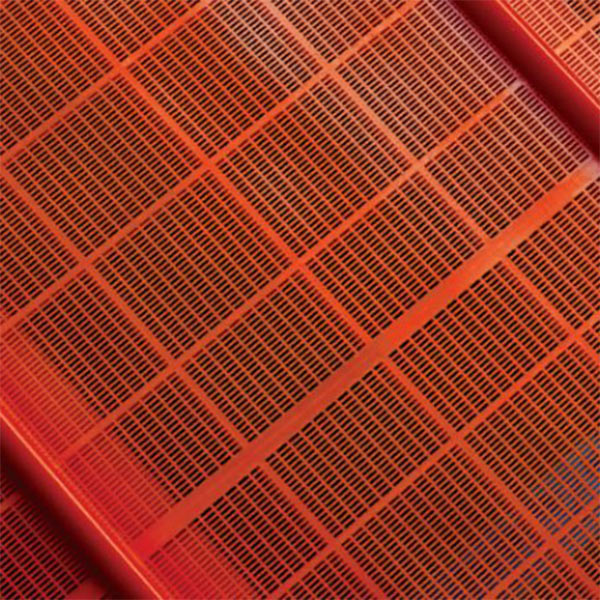
Introduction:
In today's fast-paced world, people are increasingly seeking ways to unwind and reconnect with nature. The popularity of outdoor living spaces, such as patios and decks, has surged as individuals and families look to create a tranquil environment in their own homes. Aiming to enhance this experience, one company has introduced an innovative Patio Screen Mesh that promises to transform outdoor areas into functional and comfortable living spaces.
Company Introduction:
{CompanyName}, a leading player in the home improvement industry, has a proven track record of introducing high-quality and cutting-edge products. As a company dedicated to innovation, {CompanyName} consistently strives to enhance the overall customer experience. With a focus on superior craftsmanship, design, and functionality, they have established themselves as a reliable and trusted brand.
Introducing the Patio Screen Mesh:
The new Patio Screen Mesh, developed by {CompanyName}, sets a new standard for outdoor living spaces. This groundbreaking product is specially designed to provide an optimal balance between privacy, comfort, and aesthetic appeal. By effectively shielding the area from pests, UV rays, and inclement weather, the Patio Screen Mesh transforms the patio into a versatile space that can be enjoyed throughout the year.
1. Enhanced Protection:
One of the key features of the Patio Screen Mesh is its ability to protect against unwanted elements. Mosquitoes, flies, and other insects can quickly turn a peaceful outdoor oasis into a breeding ground for annoyance. However, the unique mesh technology used by {CompanyName} acts as a protective barrier, allowing homeowners to enjoy their patios without any disturbances. It also blocks harmful UV rays, protecting individuals from excessive sun exposure while maintaining visibility and natural light.
2. Optimal Ventilation and Illumination:
The Patio Screen Mesh creates a balance between maintaining a cool and comfortable space and ample natural light and fresh air. The innovative design allows for excellent ventilation, preventing the area from becoming stuffy while still blocking out wind and other external elements. The mesh is carefully engineered to optimize airflow, enabling homeowners to enjoy the serenity of their outdoor space without being unduly affected by external weather conditions.
3. Stylish and Versatile Design:
{CompanyName}'s Patio Screen Mesh is designed with aesthetics in mind. The screens are available in a variety of colors and patterns, allowing homeowners to add a touch of personal style to their outdoor living space. The mesh seamlessly integrates into the existing patio design, maintaining its beauty and maximizing its functional potential. This versatility allows for a seamless blend with any architectural style, enhancing the overall aesthetic appeal of the patio.
4. Easy Installation and Maintenance:
Recognizing the need for convenience, {CompanyName} has ensured that the Patio Screen Mesh is easy to install and maintain. The company provides detailed installation instructions and ensures that the mesh can be easily fitted to any existing patio structure. Additionally, the durability of the mesh ensures that it requires minimal maintenance, allowing homeowners to spend more time enjoying their outdoor living spaces rather than worrying about upkeep.
Conclusion:
{CompanyName}'s revolutionary Patio Screen Mesh is set to transform outdoor living spaces across the country. With its focus on protection, ventilation, style, and ease of installation, this innovative product revolutionizes the way we enjoy our patios. By embracing the Patio Screen Mesh, homeowners can create a personalized oasis that seamlessly blends nature and comfort, enabling them to make the most of their outdoor living spaces throughout the year.
Company News & Blog
Timers: A Comprehensive Guide Electric solenoid valve timers are essential components in the automation of fluid and gas control in various industries. These timers come in different designs and functionalities to suit various applications and requirements. In this blog, we will guide you through an in-depth understanding of solenoid valve timers and their applications. What are Solenoid Valve Timers? A solenoid valve timer is an electrical device that controls the opening and closing of solenoid valves according to pre-set time intervals. The timer regulates the process flow by providing an electrical signal that triggers the solenoid valve to open, close, or partially open at precise times. They are also used to prevent system overflows, limit liquid levels, and to sequence the operation of pumps and compressors. How Do Solenoid Valve Timers Work? Solenoid valve timers operate by using an electronic timer circuit and a solenoid valve that controls the flow of fluid or gas through the valve body. The timer is pre-set to control the duration of the valve's open state. The timer circuit sends a signal to the solenoid valve, causing it to open or close. The solenoid valve is an electromechanical device that converts electrical energy into mechanical action. Applications of Solenoid Valve Timers Solenoid valve timers are used in many industries and applications, such as: 1. Irrigation Systems Solenoid valve timers are used in irrigation systems to automate the watering process. The timer controls the water flow through the solenoid valve, ensuring that plants or crops receive consistent and regulated amounts of water. 2. Industrial Automation Solenoid valve timers are used in industrial automation systems to control the flow of fluids and gases through different processes. They are also used in storage tanks, boilers, and pumps to regulate their operation. 3. HVAC Systems Heating, Ventilation, and Air Conditioning (HVAC) systems utilize solenoid valve timers to control the flow of refrigerants, coolants, and airflow. The timer regulates the timing of the cycles of the components to ensure that the system operates efficiently. 4. Medical Equipment Solenoid valve timers are used in medical equipment and laboratory applications to control the flow of fluids and gases accurately. They are commonly used in hospital laundry systems and automated laboratory equipment. Factors to Consider When Choosing a Solenoid Valve Timer When selecting a solenoid valve timer, you must consider the following factors: 1. Timer Type Solenoid valve timers come in different types, including on-delay, off-delay, pulse, and interval timer types. Each type has its unique function and duration, depending on the application requirements. 2. Timing Range The timing range is the number of seconds, minutes, or hours that the solenoid valve remains open or closed. Consider the timing range of the timer according to the application. 3. Power Requirements The timer power requirements should match those of the solenoid valve or the equipment the timer is controlling. Select a timer that operates on the required voltage and frequency. 4. Interface and Mounting Ensure that the timer has an interface and mounting design that suits the device or system it will control. Conclusion Solenoid valve timers are essential in the automation of fluid and gas control processes in various industries. Understanding their functions and applications is crucial in selecting the right type of timer for your system. Remember to consider the timing range, power requirements, interface, and mounting design when selecting a solenoid valve timer for your application. In summary, electric solenoid valve timers are critical in the control and regulation of fluid and gas flow in many applications. Tameson offers a wide range of solenoid valve timers suitable for various industries. Browse our website or contact us for more information.
Discover the Advantages of Using a Reliable Sifting Screen Mesh
Title: Revolutionary Sifting Screen Mesh Introduces Cutting-Edge Innovation to Improve Industrial Materials SortingIntroduction:The materials sorting process has always been a crucial aspect of various industrial sectors. From mining and construction to food processing and recycling, the efficient separation of materials is vital for achieving high-quality end products. In a groundbreaking development, an innovative sifting screen mesh has been introduced by a renowned company dedicated to revolutionizing the materials sorting industry.Company Introduction: (Please provide specific details about the company to complete this section)[Company Name], a leading player in the materials sorting industry, has been at the forefront of developing advanced solutions for efficient and precise material separation. With decades of experience, cutting-edge research and development, and a commitment to customer satisfaction, [Company Name] has established itself as an industry leader.Main News Content:Para 1:[Company Name] has recently unveiled a new sifting screen mesh, designed to enhance the materials sorting process in various industries. The innovative mesh has been developed after extensive research and testing, aiming to address the common challenges faced by industrial operators during material separation.Para 2:Traditionally, materials sorting has relied on conventional meshes that are vulnerable to quick wear and tear, resulting in compromised efficiency and increased operational costs. However, the newly introduced sifting screen mesh is engineered to offer unparalleled durability, ensuring extended service life without compromising performance.Para 3:One of the key features that set this advanced mesh apart from its predecessors is its composition. The mesh is constructed from a unique blend of high-quality alloys that exhibit exceptional tensile strength, corrosion resistance, and anti-wearing properties. These characteristics enable the mesh to withstand the rigorous demands of industrial sorting operations, reducing the need for frequent replacements and repair.Para 4:The sifting screen mesh also incorporates a meticulously designed filtration system, aimed at optimizing sorting accuracy. The precisely engineered apertures ensure efficient separation of materials based on size, shape, and density, enabling operators to obtain consistent and high-quality end products. This improved accuracy significantly reduces material wastage and enhances productivity.Para 5:Moreover, [Company Name]'s sifting screen mesh is available in a wide range of mesh sizes, enabling customization to suit specific sorting requirements across various industries. This flexibility allows operators to achieve precise separation even with varied material types and particle sizes.Para 6:Recognizing the need for environmentally friendly solutions, [Company Name] has ensured that their sifting screen mesh is easily recyclable. By employing recyclable materials, the company demonstrates its commitment to sustainability, aligning with global efforts towards minimizing carbon footprints.Para 7:Additionally, [Company Name] offers comprehensive customer support services to ensure the seamless integration of the new sifting screen mesh into existing operations. Expert technicians provide guidance on installation, maintenance, and troubleshooting, ensuring optimized performance and prolonging the lifespan of the mesh.Para 8:Given the promising potential of the new sifting screen mesh, [Company Name] has already received overwhelmingly positive feedback from early adopters. The enhanced durability, accuracy, and sustainability of the mesh have attracted a significant number of industries seeking to improve their materials sorting processes.Conclusion:In an era where efficiency and sustainability are paramount, [Company Name]'s introduction of the revolutionary sifting screen mesh represents a significant leap forward in the materials sorting industry. By combining durability, accuracy, customization, and recyclability, this innovative product promises to optimize materials separation processes across various industrial sectors. As [Company Name] continues to push boundaries, it stands ready to revolutionize the way companies sort materials, ultimately contributing to increased productivity and decreased environmental impact.
Different Techniques for Examining Oil Casing - a Manufacturer of Steel Pipes
Oil and gas drilling is a complex process that involves various safety measures and technical considerations. One of the crucial components of drilling operations is the casing pipe that keeps the wellbore intact and prevents any leaks or collapses. Seamless casing pipes are preferred for their durability, strength, and resistance to corrosion and other environmental factors. In this blog post, we will discuss the various inspection methods used to ensure the quality and safety of seamless casing pipes.Visual InspectionVisual inspection is the most basic form of inspection that involves examining the exterior and interior surfaces of the casing pipe for any visible defects or damages. An inspector checks for any cracks, dents, corrosion, or other signs of wear and tear that can compromise the integrity of the pipe. They also ensure that the length, diameter, and thickness of the pipe are as per the specifications and the markings are correct.Ultrasonic TestingUltrasonic testing (UT) is a non-destructive testing (NDT) method that uses high-frequency sound waves to detect any flaws or defects in the casing pipe. The inspector uses a handheld device called a UT probe that sends and receives sound waves through the pipe wall. The waves reflect back differently depending on the thickness, density, and location of any discontinuities or anomalies, which the device records and displays on a monitor or chart.Magnetic Particle InspectionMagnetic particle inspection (MPI) is another NDT method that uses magnetic fields and iron oxide particles to locate any surface or subsurface cracks or defects in the casing pipe. The inspector applies a magnetic field to the pipe and sprinkles iron oxide particles on the surface. If there are any cracks or flaws, the particles will accumulate there and form a visible indication or pattern. The inspector can interpret the pattern and determine the type, size, and location of the defects.Liquid Penetrant InspectionLiquid penetrant inspection (LPI) is an NDT method that uses a dye or fluorescent liquid to detect any surface cracks or discontinuities in the casing pipe. The inspector applies the liquid to the surface and waits for it to seep into any openings. After wiping off the excess, they apply a developer that draws the liquid back to the surface and forms a visible indication or pattern. The inspector can then evaluate the pattern and determine the extent and severity of the defects.Eddy Current TestingEddy current testing (ECT) is an NDT method that uses electromagnetic fields to detect any surface or subsurface defects in the casing pipe. The inspector uses a handheld device called an eddy current probe that creates a magnetic field around the pipe. Any changes in the field caused by defects or anomalies will induce currents that the probe detects and records. The inspector can then analyze the data and determine the type, size, and location of the defects.ConclusionSeamless casing pipes are vital components of oil and gas drilling operations that require strict quality control and safety measures. Various inspection methods such as visual inspection, ultrasonic testing, magnetic particle inspection, liquid penetrant inspection, and eddy current testing can detect any defects or flaws in the casing pipe and ensure their integrity and reliability. As a leading seamless casing pipe manufacturer, we adhere to the highest standards of quality and craftsmanship to deliver the best products to our clients. Contact us if you have any inquiries or requirements for seamless casing pipes.
Discover the Benefits of Fiber Expansion Joints for Enhanced Structural Flexibility
Fiber Expansion Joint: An Innovative Solution for Construction Needs Construction is one of the most fast-paced and constantly evolving industries in the world. With the rise of new technologies and innovations, it has become more important than ever to keep up with the latest trends and developments in order to ensure the highest standards of quality and safety for construction projects. One of the latest trends in construction is the use of fiber expansion joints, a novel and versatile solution for addressing the challenges of movement and stress in concrete structures. Fiber expansion joints are designed to absorb movement caused by temperature changes, settlement, and other factors that can cause cracking or failure in concrete structures. They are made of high-quality fibers and bonded together with a specialized resin, creating a strong and durable material that can withstand extreme weather conditions and heavy loads. Fiber expansion joints have several advantages over traditional expansion joints, including improved strength, flexibility, and ease of installation. One of the leading manufacturers of fiber expansion joints is a company based in the United States. This company has been at the forefront of the fiber expansion joint industry, developing innovative products and solutions that meet the diverse needs of construction professionals around the world. With over 40 years of experience in the field, this company has become a trusted partner for customers in a wide range of industries, from infrastructure and transportation to commercial and industrial construction. The fiber expansion joints produced by this company are designed to meet the highest standards of quality and durability. They are subjected to rigorous testing and quality control measures throughout the manufacturing process, ensuring that each product meets the exacting requirements of customers. The company uses state-of-the-art technology and equipment to produce fiber expansion joints that are both strong and flexible, providing reliable protection against movement and stress in concrete structures. In addition to their superior strength and flexibility, fiber expansion joints from this company are also easy to install and maintain. They come in a wide range of sizes and configurations, allowing construction professionals to choose the right product for their specific needs. Installation is quick and straightforward, with no special tools or skills required. And once installed, fiber expansion joints require minimal maintenance, providing long-lasting protection and cost-effective performance over the life of the structure. The advantages of using fiber expansion joints in construction projects are clear. They offer superior protection against movement and stress, helping to prevent cracking and failure in concrete structures. They are also cost-effective and easy to install, making them an attractive option for construction professionals looking to save time and money on their projects. With their extensive experience and expertise in the field, the company behind fiber expansion joints is a valuable partner for any construction project, providing innovative solutions and quality products that meet the highest standards of performance and reliability. Overall, the use of fiber expansion joints represents a major step forward in the evolution of the construction industry. As new challenges and demands emerge in the field, it is important to embrace innovative solutions like fiber expansion joints that can help to improve safety, reduce costs, and enhance the overall quality of construction projects. With their wide range of benefits and excellent track record of performance, fiber expansion joints are sure to become a standard feature in construction projects around the world. For anyone involved in construction, it is essential to stay up-to-date on the latest developments in the field and to seek out innovative solutions like fiber expansion joints that can help to ensure the success of projects both large and small.
Essential Guide to Gate Valves: All You Need to Know
Title: Innovative Gate Valve Enhances Efficiency and Safety in Industrial OperationsIntroduction:In the fast-evolving industrial landscape, the need for reliable and efficient equipment has become paramount. One such equipment that plays a crucial role in ensuring smooth operations is the gate valve. Designed to control and regulate the flow of fluids, this essential component has been further perfected by an industry-leading company, revolutionizing the way industries operate. In this article, we will explore the exceptional features and benefits of this innovative gate valve, while diving into the company behind its groundbreaking advancements.Overview of the Gate Valve:The newly developed gate valve, known for its cutting-edge technology and remarkable performance, has set new standards in the industry. Engineered to cater to the diverse needs of various applications within sectors such as oil and gas, water treatment, power plants, and chemical processing, this valve promises unparalleled efficiency and safety.1. Enhanced Design and Functionality:The gate valve boasts an advanced design that enables seamless operation and precise fluid control. It consists of a sliding gate, also referred to as a disc, which moves up and down within the valve body to either restrict or allow fluid flow. This state-of-the-art design ensures minimal friction and pressure loss, resulting in increased efficiency and reduced energy consumption.2. Robust Construction:Crafted from high-quality materials, the gate valve excels in durability, making it suitable for even the harshest industrial environments. The valve's body and disc are composed of rugged metals, ensuring resistance against corrosion, wear, and tear. Additionally, the valve's sturdy construction helps minimize the risk of leaks and premature failures, guaranteeing enhanced safety and extended operational lifespan.3. Excellent Flow Control:By incorporating precision-engineered sealing features, the gate valve delivers exceptional flow control capabilities. The sliding gate mechanism enables the valve to achieve a tight seal when in the closed position, preventing any unwanted leakage. This ensures a reliable and secure flow control system, safeguarding valuable resources, and protecting the environment.Company Introduction:The company behind these remarkable advancements in gate valve technology is a renowned global leader in fluid control solutions. With decades of experience and a commitment to innovation, this company has successfully established itself as a trusted partner for industries worldwide.A. Commitment to Quality:Recognizing the critical role played by valves in industrial processes, the company upholds rigorous quality standards throughout the manufacturing process. Each valve undergoes stringent testing procedures, adhering to international safety and performance regulations. This dedication to quality ensures that the gate valve delivers optimum results in terms of reliability, accuracy, and longevity.B. Research and Development:Investing heavily in research and development, the company continues to drive innovation in fluid control technology. By collaborating with industry experts and utilizing cutting-edge facilities, the company consistently develops state-of-the-art solutions that address the evolving needs of diverse industrial sectors. This commitment to advancement positions the company as an industry trailblazer, constantly pushing the boundaries of what is possible.C. Customer-Centric Approach:With a customer-centric philosophy at its core, the company focuses on providing tailored solutions to meet specific requirements. By actively engaging with clients, understanding their challenges, and offering comprehensive technical support, the company ensures customer satisfaction and builds long-lasting partnerships. Additionally, a responsive after-sales service network guarantees quick assistance and swift resolution of any issues that may arise.Conclusion:The introduction of the innovative gate valve, coupled with the company's relentless pursuit of excellence, marks an important milestone in the evolution of fluid control technology. With its advanced design, robust construction, and exceptional flow control capabilities, this gate valve is set to redefine efficiency and safety standards in industrial operations. As the company continues to lead through research and development, their dedication to quality and customer satisfaction solidifies their position as a driving force in the fluid control solutions industry.
How Conveyor Pulleys Drive the Power of Industries" can be rewritten as "Discovering the Power of Conveyor Pulleys in the Industry.
Conveyor Pulley Company Streamlines Manufacturing Process with Latest TechnologyConveyor pulleys are an essential component of any conveyor belt system. They are responsible for supporting the weight of the belt, providing traction to the belt, and guiding the belt to ensure that it moves smoothly and efficiently. As such, conveyor pulleys play an important role in the overall performance of a conveyor system.One company that has been manufacturing conveyor pulleys for more than 25 years is {insert company name}. Over the years, the company has developed a reputation for producing high-quality pulleys that are reliable, durable, and effective. And now, thanks to the latest technology, the company has streamlined its manufacturing process even further, making its pulleys even more efficient and reliable than ever before.The company's commitment to quality is evident in its use of state-of-the-art technology and equipment. For example, the company uses computer-aided design (CAD) technology to design its pulleys down to a microscopic level, ensuring that each one is precisely engineered to meet the customer's requirements. The company's manufacturing process also includes cutting-edge machinery such as CNC lathes and milling machines, which allow the company to produce pulleys with extreme precision.One of the most significant advancements in the company's manufacturing process is its use of a new hydraulic press. The press, which is capable of exerting up to 150 tons of pressure, allows the company to form its pulleys with more accuracy and consistency than ever before. As a result, the pulleys that come off the company's assembly line are of the highest quality and are able to deliver superior performance over an extended period of time.The company's commitment to quality extends beyond its products to include its customer service as well. For example, the company's engineers work closely with customers to design pulleys that are tailored to their specific needs. The company also offers on-site installation and maintenance services, ensuring that its customers get the most out of their conveyor systems.In addition to its commitment to quality, the company is also dedicated to sustainability. The company uses environmentally-friendly materials and processes wherever possible, and it is always looking for ways to reduce its carbon footprint.Overall, the combination of state-of-the-art technology, commitment to quality, and dedication to sustainability has made {insert company name} one of the leading conveyor pulley manufacturers in the industry. With its streamlined manufacturing processes, the company is able to produce superior-quality pulleys that are highly efficient, reliable, and sustainable. As the company continues to push the boundaries of technology and innovation, it is sure to remain at the forefront of the industry for years to come.
Expert Tips for Conveyor Belt Splicing Techniques: Best Methods Revealed
Tips and Procedures for Splicing Conveyor Belts: Why Hot Vulcanization is RecommendedConveyor belts play a critical role in the transportation of varying products in different manufacturing and industrial settings. With the constant use of conveyor belts, it's inevitable that they will eventually wear and tear, break, and require repair. In such moments, conveyor belt splicing is essential.Several methods can be used to splice conveyor belts, including mechanical splicing and hot vulcanization. However, when it comes to choosing the best option, experts recommend hot vulcanization. This method involves the use of heat and pressure to bond the repair material to the damaged area, making it a durable, strong, and long-lasting solution.Why Choose Hot Vulcanization?Although hot vulcanization is more expensive and takes longer than mechanical splicing, it offers numerous benefits. Some of these benefits include:1. High Quality and Long-Lasting RepairsHot vulcanization enables you to achieve high-quality, long-lasting conveyor belt splicing solutions. The vulcanized splice is strong, durable, and often outlasts the original belt. The method ensures that you don't have to worry about conveyor downtime due to belt failure.2. Improved SafetyImproved safety is a significant benefit of vulcanized conveyor splicing. The process helps ensure that the conveyor belt is strong and direct to avoid accidents in the workplace. A damaged conveyor belt can result in injury or accidents that can cause significant damage to personnel, facilities, machinery, and products.3. Increased Conveyor EfficiencyVulcanized conveyor belt splicing helps optimize conveyor efficiency by minimizing downtime and reducing maintenance costs. This implies that you can focus more on production and less on conveyor maintenance, repair, and replacement.Procedures for Hot Vulcanization of Conveyor BeltsVulcanizing a conveyor belt involves several steps, including preparation, curing, and finishing. Here is a step-by-step guide to hot vulcanizing conveyor belts:1. Preparationa) Clean the damaged area by removing any dirt or debris.b) Mark the damaged section of the belt using a chalk or marker.c) Cut along the marked section using a repair strip cutter.d) Trim the end of the cut to make the repair strip neat.e) Buff both the belt and repair strip with a grinder to create a smooth surface.2. Curinga) Lay the belt ends together on a curing table and ensure that the splices are square.b) Apply hot vulcanizing material to both the belt ends.c) Use a putty knife to spread the material evenly.d) Position the repair strip and ensure that it covers the entire damaged area.e) Cover the repair strip with a release cloth.f) Use a vulcanizer to heat the splice to cure the hot vulcanizing material.3. Finishinga) Remove the release cloth.b) Cut any excess material from around the splice.c) By using a pry bar, carefully remove the splicing frame.d) Finally, inspect the conveyor belt to ensure the splice is cured correctly.In conclusion, conveyor belt splicing is a crucial process that should be taken seriously to ensure that the conveyor system operates smoothly and efficiently. Although there are several different belt splicing methods, hot vulcanization is the most reliable and durable solution. Following the proper hot vulcanization procedures will guarantee a high-quality repair that will last for an extended period.
Efficient and Versatile Conveyor Systems with Geared and Motorised Options
Belt conveyors are an essential part of various manufacturing processes, allowing for the transportation of goods from one place to another with ease. The conveyors are made up of several components that work together to ensure a smooth and efficient operation. One such component is the conveyor belt drum roller.Conveyor belt drum rollers are cylindrical rollers that are typically used to support a conveyor belt and ensure that it moves smoothly. They are also known as drive rollers, and their main purpose is to provide the driving force needed to move the belt. The drum roller is typically made from materials such as steel or rubber, and it is mounted on a shaft that is driven by a motor.The Fastrax conveyor rollers provide geared motor and motorised drum motor drive options, which offer a more efficient and reliable conveyor system. The geared motor option consists of a motor that is connected to a gearbox, which provides the necessary torque to drive the drum roller. The motorised drum motor drive option is a self-contained motor and gearbox unit that is mounted directly onto the drum roller.One of the benefits of using a motorised drum motor drive is that it eliminates the need for external drive components, such as chains and sprockets. This makes the conveyor system more compact and easier to maintain. The motorised drum motor drive also provides precise control over the conveyor belt speed, ensuring that the goods are transported at the desired rate.In addition to the drive options, Fastrax conveyor rollers feature mild steel, powder-coated frames. This gives the rollers extra durability and protects them from wear and tear, making them suitable for use in various industrial applications.Overall, conveyor belt drum rollers play an essential role in conveyor systems, providing the driving force needed to move the conveyor belt and transport goods. The Fastrax conveyor rollers, with their geared motor and motorised drum motor drive options and durable frames, are a reliable and efficient solution for manufacturing and other industrial processes that require the use of conveyor systems.In conclusion, conveyor belt drum rollers are an integral part of modern manufacturing processes. The Fastrax conveyor rollers, with their advanced drive options and durable frames, provide a reliable and efficient solution for conveyor systems. If you are in the market for a conveyor system, be sure to consider the Fastrax conveyor rollers and the benefits they can offer to your production line.
Timers: A Comprehensive Guide Electric solenoid valve timers are essential components in the automation of fluid and gas control in various industries. These timers come in different designs and functionalities to suit various applications and requirements. In this blog, we will guide you through an in-depth understanding of solenoid valve timers and their applications. What are Solenoid Valve Timers? A solenoid valve timer is an electrical device that controls the opening and closing of solenoid valves according to pre-set time intervals. The timer regulates the process flow by providing an electrical signal that triggers the solenoid valve to open, close, or partially open at precise times. They are also used to prevent system overflows, limit liquid levels, and to sequence the operation of pumps and compressors. How Do Solenoid Valve Timers Work? Solenoid valve timers operate by using an electronic timer circuit and a solenoid valve that controls the flow of fluid or gas through the valve body. The timer is pre-set to control the duration of the valve's open state. The timer circuit sends a signal to the solenoid valve, causing it to open or close. The solenoid valve is an electromechanical device that converts electrical energy into mechanical action. Applications of Solenoid Valve Timers Solenoid valve timers are used in many industries and applications, such as: 1. Irrigation Systems Solenoid valve timers are used in irrigation systems to automate the watering process. The timer controls the water flow through the solenoid valve, ensuring that plants or crops receive consistent and regulated amounts of water. 2. Industrial Automation Solenoid valve timers are used in industrial automation systems to control the flow of fluids and gases through different processes. They are also used in storage tanks, boilers, and pumps to regulate their operation. 3. HVAC Systems Heating, Ventilation, and Air Conditioning (HVAC) systems utilize solenoid valve timers to control the flow of refrigerants, coolants, and airflow. The timer regulates the timing of the cycles of the components to ensure that the system operates efficiently. 4. Medical Equipment Solenoid valve timers are used in medical equipment and laboratory applications to control the flow of fluids and gases accurately. They are commonly used in hospital laundry systems and automated laboratory equipment. Factors to Consider When Choosing a Solenoid Valve Timer When selecting a solenoid valve timer, you must consider the following factors: 1. Timer Type Solenoid valve timers come in different types, including on-delay, off-delay, pulse, and interval timer types. Each type has its unique function and duration, depending on the application requirements. 2. Timing Range The timing range is the number of seconds, minutes, or hours that the solenoid valve remains open or closed. Consider the timing range of the timer according to the application. 3. Power Requirements The timer power requirements should match those of the solenoid valve or the equipment the timer is controlling. Select a timer that operates on the required voltage and frequency. 4. Interface and Mounting Ensure that the timer has an interface and mounting design that suits the device or system it will control. Conclusion Solenoid valve timers are essential in the automation of fluid and gas control processes in various industries. Understanding their functions and applications is crucial in selecting the right type of timer for your system. Remember to consider the timing range, power requirements, interface, and mounting design when selecting a solenoid valve timer for your application. In summary, electric solenoid valve timers are critical in the control and regulation of fluid and gas flow in many applications. Tameson offers a wide range of solenoid valve timers suitable for various industries. Browse our website or contact us for more information.
Discover the Advantages of Using a Reliable Sifting Screen Mesh
Title: Revolutionary Sifting Screen Mesh Introduces Cutting-Edge Innovation to Improve Industrial Materials SortingIntroduction:The materials sorting process has always been a crucial aspect of various industrial sectors. From mining and construction to food processing and recycling, the efficient separation of materials is vital for achieving high-quality end products. In a groundbreaking development, an innovative sifting screen mesh has been introduced by a renowned company dedicated to revolutionizing the materials sorting industry.Company Introduction: (Please provide specific details about the company to complete this section)[Company Name], a leading player in the materials sorting industry, has been at the forefront of developing advanced solutions for efficient and precise material separation. With decades of experience, cutting-edge research and development, and a commitment to customer satisfaction, [Company Name] has established itself as an industry leader.Main News Content:Para 1:[Company Name] has recently unveiled a new sifting screen mesh, designed to enhance the materials sorting process in various industries. The innovative mesh has been developed after extensive research and testing, aiming to address the common challenges faced by industrial operators during material separation.Para 2:Traditionally, materials sorting has relied on conventional meshes that are vulnerable to quick wear and tear, resulting in compromised efficiency and increased operational costs. However, the newly introduced sifting screen mesh is engineered to offer unparalleled durability, ensuring extended service life without compromising performance.Para 3:One of the key features that set this advanced mesh apart from its predecessors is its composition. The mesh is constructed from a unique blend of high-quality alloys that exhibit exceptional tensile strength, corrosion resistance, and anti-wearing properties. These characteristics enable the mesh to withstand the rigorous demands of industrial sorting operations, reducing the need for frequent replacements and repair.Para 4:The sifting screen mesh also incorporates a meticulously designed filtration system, aimed at optimizing sorting accuracy. The precisely engineered apertures ensure efficient separation of materials based on size, shape, and density, enabling operators to obtain consistent and high-quality end products. This improved accuracy significantly reduces material wastage and enhances productivity.Para 5:Moreover, [Company Name]'s sifting screen mesh is available in a wide range of mesh sizes, enabling customization to suit specific sorting requirements across various industries. This flexibility allows operators to achieve precise separation even with varied material types and particle sizes.Para 6:Recognizing the need for environmentally friendly solutions, [Company Name] has ensured that their sifting screen mesh is easily recyclable. By employing recyclable materials, the company demonstrates its commitment to sustainability, aligning with global efforts towards minimizing carbon footprints.Para 7:Additionally, [Company Name] offers comprehensive customer support services to ensure the seamless integration of the new sifting screen mesh into existing operations. Expert technicians provide guidance on installation, maintenance, and troubleshooting, ensuring optimized performance and prolonging the lifespan of the mesh.Para 8:Given the promising potential of the new sifting screen mesh, [Company Name] has already received overwhelmingly positive feedback from early adopters. The enhanced durability, accuracy, and sustainability of the mesh have attracted a significant number of industries seeking to improve their materials sorting processes.Conclusion:In an era where efficiency and sustainability are paramount, [Company Name]'s introduction of the revolutionary sifting screen mesh represents a significant leap forward in the materials sorting industry. By combining durability, accuracy, customization, and recyclability, this innovative product promises to optimize materials separation processes across various industrial sectors. As [Company Name] continues to push boundaries, it stands ready to revolutionize the way companies sort materials, ultimately contributing to increased productivity and decreased environmental impact.
Different Techniques for Examining Oil Casing - a Manufacturer of Steel Pipes
Oil and gas drilling is a complex process that involves various safety measures and technical considerations. One of the crucial components of drilling operations is the casing pipe that keeps the wellbore intact and prevents any leaks or collapses. Seamless casing pipes are preferred for their durability, strength, and resistance to corrosion and other environmental factors. In this blog post, we will discuss the various inspection methods used to ensure the quality and safety of seamless casing pipes.Visual InspectionVisual inspection is the most basic form of inspection that involves examining the exterior and interior surfaces of the casing pipe for any visible defects or damages. An inspector checks for any cracks, dents, corrosion, or other signs of wear and tear that can compromise the integrity of the pipe. They also ensure that the length, diameter, and thickness of the pipe are as per the specifications and the markings are correct.Ultrasonic TestingUltrasonic testing (UT) is a non-destructive testing (NDT) method that uses high-frequency sound waves to detect any flaws or defects in the casing pipe. The inspector uses a handheld device called a UT probe that sends and receives sound waves through the pipe wall. The waves reflect back differently depending on the thickness, density, and location of any discontinuities or anomalies, which the device records and displays on a monitor or chart.Magnetic Particle InspectionMagnetic particle inspection (MPI) is another NDT method that uses magnetic fields and iron oxide particles to locate any surface or subsurface cracks or defects in the casing pipe. The inspector applies a magnetic field to the pipe and sprinkles iron oxide particles on the surface. If there are any cracks or flaws, the particles will accumulate there and form a visible indication or pattern. The inspector can interpret the pattern and determine the type, size, and location of the defects.Liquid Penetrant InspectionLiquid penetrant inspection (LPI) is an NDT method that uses a dye or fluorescent liquid to detect any surface cracks or discontinuities in the casing pipe. The inspector applies the liquid to the surface and waits for it to seep into any openings. After wiping off the excess, they apply a developer that draws the liquid back to the surface and forms a visible indication or pattern. The inspector can then evaluate the pattern and determine the extent and severity of the defects.Eddy Current TestingEddy current testing (ECT) is an NDT method that uses electromagnetic fields to detect any surface or subsurface defects in the casing pipe. The inspector uses a handheld device called an eddy current probe that creates a magnetic field around the pipe. Any changes in the field caused by defects or anomalies will induce currents that the probe detects and records. The inspector can then analyze the data and determine the type, size, and location of the defects.ConclusionSeamless casing pipes are vital components of oil and gas drilling operations that require strict quality control and safety measures. Various inspection methods such as visual inspection, ultrasonic testing, magnetic particle inspection, liquid penetrant inspection, and eddy current testing can detect any defects or flaws in the casing pipe and ensure their integrity and reliability. As a leading seamless casing pipe manufacturer, we adhere to the highest standards of quality and craftsmanship to deliver the best products to our clients. Contact us if you have any inquiries or requirements for seamless casing pipes.