Applications of Single Sphere Rubber Expansion Joints in Various Industries
By:Admin
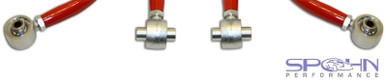
Henan Shunying is a renowned manufacturer of industrial rubber products that offers a wide range of expansion joints, including single sphere rubber expansion joints. These types of expansion joints are typically used in various applications to prevent damage to the attached equipment, limit noise transmission, and reduce vibration caused by thermal expansion, pipeline misalignment, and ground settlement.
Single sphere rubber expansion joints are designed to withstand large movements and pressure fluctuations. The single sphere feature helps it to absorb noise, decrease vibration, and compensate for slight misalignments. The joints are made of high-quality EPDM or NBR rubber, which is flexible, resilient and durable, and is resistant to water, heat, chemicals, and UV rays. This makes them ideal for a wide range of applications, especially in industrial and mechanical environments.
The features of Single Sphere Rubber Expansion Joint
Single sphere rubber expansion joints have several features that have made them popular in various industries such as chemical, petroleum, power generation, pharmaceuticals, mining, steel, water treatment, and HVAC.
1. Flexibility:
Flexibility is an essential feature of these expansion joints as it ensures that they can compensate for any axial, lateral or angular movements in the piping system. The flexible nature of the expansion joint helps reduce the risk of fatigue and cracking in pipelines and equipment.
2. High-pressure resistance:
Single sphere rubber joints are designed to withstand high-pressure applications, making them ideal for situations where pressure fluctuations occur regularly. They can withstand high bursts of pressure, thereby reducing the risk of equipment damage and potential leaks.
3. Absorption of movements and vibrations:
Single sphere rubber expansion joints are known for their ability to absorb movements and vibrations, reducing the risk of damage to connected equipment. Their ability to absorb vibrations also helps reduce noise transmission, which is essential in many industrial applications.
4. Easy installation:
Installation of single sphere rubber expansion joints is straightforward and requires minimal equipment. They are designed to fit perfectly into the pipeline, allowing for easy installation in limited spaces and hard-to-reach areas.
5. Durability:
Single sphere rubber expansion joints are durable and can withstand harsh working environments such as high temperatures, corrosive chemicals and UV radiation. They have a long lifespan and require minimal maintenance, making them cost-effective in the long run.
Applications for Single Sphere Rubber Expansion Joint
Single sphere rubber expansion joints are typically used in situations where pipeline misalignment, ground settlement or thermal expansion is expected, which includes the following applications:
1. HVAC:
Single sphere rubber expansion joints are commonly used in the HVAC industry, where they absorb thermal movements and vibrations caused by hot and cold air. Their flexibility also provides a seal between the air ducts and the equipment, reducing noise levels.
2. Mining:
Mining operations require flexible piping systems that can withstand harsh industrial environments. The single sphere rubber expansion joint is widely used in mining sites and can absorb excess vibrations and movements in the pipeline, reducing the risk of damage to equipment.
3. Power generation:
Single sphere rubber expansion joints are also used in power generation plants to reduce the risk of thermal expansion. They can also absorb vibrations from machinery, reducing noise, and prolonging the lifespan of connected equipment.
4. Chemical plants:
In chemical plants, the expansion joints can withstand corrosive chemicals as they are resistant to a wide range of chemicals, including acids, alkalis, and solvents, making them perfect for pipe connections.
Conclusion
Single sphere rubber expansion joints are an essential component of an industrial piping system. They play an integral role in reducing the risk of damage to connected equipment, limiting noise transmission, and reducing vibration caused by thermal expansion, pipeline misalignment, and ground settlement. The Henan Shunying Single sphere rubber expansion joint is a quality product that offers flexibility, high-pressure resistance, easy installation, durability, and is suitable for various applications. In conclusion, the single sphere rubber expansion joint is a reliable solution that is both cost-effective and long-lasting.
Company News & Blog
Flexible and Waterproof Expansion Joints for Asphalt Construction
and Expansion Joint Filler.Asphalt expansion joints are an essential component of road construction. They act as a buffer between different sections of the road, allowing for the natural expansion and contraction that occurs due to temperature changes. Without expansion joints, roads would have a tendency to buckle and crack, leading to costly repairs and safety hazards. In this blog post, we will explore the benefits of using asphalt expansion joints and why the use of an expansion joint filler is crucial.As mentioned earlier, asphalt expansion joints are necessary for the proper functioning of any road. They allow for the natural expansion and contraction of the road surface, which prevents it from cracking and becoming uneven. Expansion joints also play a vital role in managing water run-off. They keep water from seeping into the ground and causing damage to the road's substructure. As such, it's important to choose an expansion joint material that is durable, weather-resistant, and long-lasting.One of the most popular expansion joint fillers used in the construction industry today is the Asphalt Expansion Joint. Its composition of blended asphalts and mineral fillers make it waterproof, flexible, permanent, and self-sealing. These properties make it an excellent option for use in a variety of road construction projects.The Asphalt Expansion Joint is designed to withstand a range of temperature changes without losing its efficacy. The heat and pressure applied during its creation ensure that it remains pliable in both hot and cold weather. This ability to withstand temperature changes makes it a natural choice for use in climates that experience extreme weather conditions.Another major advantage of this expansion joint material is its ability to self-seal. This means that if there is any damage to the joint, it will automatically seal itself, preventing water from entering the road's substructure and causing damage. This option is particularly useful in areas where repairs are not easily accessible. The self-sealing nature of the Asphalt Expansion Joint ensures that roads remain safe and secure for an extended period.ConclusionAsphalt Expansion Joints are an indispensable part of any road construction project. They ensure the safety, durability, and longevity of roads by preventing cracking, buckling, and unevenness. The Asphalt Expansion Joint, in particular, is an excellent choice for expansion joint filler due to its versatile composition, making it waterproof, flexible, permanent, and self-sealing. This unique blend of properties makes it an excellent option for use in a variety of highway construction projects. By selecting the right expansion joint material, construction companies can build safer, longer-lasting roads that can withstand the test of time and extreme weather conditions.
Rubber Air Hose with 1/4-Inch MPT Ends and Bend Restrictors Offers High Performance for Air Tools
Telescoping Flanged Fittings for Simplified Retrofitting Applications
Dismantling Joint for HDPE Pipe – The Solution for Retrofitting ApplicationsA flanged pipe system is an essential component of a fluid transfer system. However, in retrofitting applications, adding, repairing or replacing flanged fittings can be a challenging task. Traditional methods require cutting of the flange, removal of bolts, and breaking the joint to take out the damaged fittings. This approach involves high cost, labor, and downtime. To overcome this challenge, engineers have developed a solution in the form of Dismantling Joint for HDPE Pipe.A Dismantling Joint for HDPE Pipe is a special type of joint that allows the disassembly and reassembly of flanged pipe systems without cutting or breaking the pipe. It is suitable for retrofitting applications where the replacement of flanged fittings is necessary. The joint consists of two halves that can be separated without disrupting the pipeline's flow. The halves are held together by bolts, nuts, and a sealing gasket that ensures tightness and prevents leaks.The joint provides several advantages over traditional methods. With the Dismantling Joint, the installation and replacement of flanged fittings become more manageable, less time-consuming, and more cost-effective. Unlike traditional methods that require cutting of the flange, the joint eliminates the need for cutting and welding of the pipe, resulting in less downtime and disruption. Additionally, the joint's modular design allows for fast and easy assembly and disassembly, reducing labor costs.Another important advantage of the Dismantling Joint is its superior performance. The joint has a telescopic design that allows for flexibility in movement, expansion, and contraction of the pipeline. This feature makes it suitable for applications that involve temperature variations or ground movement. The joint's flexibility ensures that the system remains stable and permanent, preventing leaks and minimizing the risk of failure.The Dismantling Joint also provides versatility in its application. It can be used for various pipe materials, including HDPE, PVC, and cast iron, making it a go-to solution for retrofitting applications. The joint is also compatible with various flange standards, including ANSI, DIN, BS, and JIS, providing a solution for a wide range of piping systems.In conclusion, retrofitting applications involving flanged pipe systems require a solution that is easy to install, cost-effective, and reliable. The Dismantling Joint for HDPE Pipe provides the solution for adding, repairing, or replacing flanged fittings within a flanged pipe system. Its modular design, flexibility, and compatibility make it a versatile solution suitable for the majority of retrofitting applications.Therefore, if you are looking for a solution for your retrofitting application, consider the Dismantling Joint for HDPE Pipe. It reduces downtime, labor costs, and ensures long-term stability and reliability of your piping system. Remember, seamless fluid transfer depends on the quality of your piping system, and the Dismantling Joint for HDPE Pipe is one step closer towards achieving that goal.
Pipe Lining and Coating: Why Polyurethane Lined Steel Pipe is the Way to GoPipe lining and coating have become increasingly important in the realm of infrastructure repair and maintenance. With aging pipelines and increased demand for water and waste water treatment, it is crucial to protect and revamp these systems to prevent environmental damage, contamination, and loss of valuable resources.At Vulcan Painters, we specialize in coating ductile iron pipe, steel pipe, and structural steel, as well as tanks and water and waste water equipment at sewage treatment facilities. Our expertise in pipe lining and coating has allowed us to become a trusted name in the industry, providing high-quality services that ensure the longevity and safety of pipelines.One type of pipe lining that we highly recommend for steel pipelines is polyurethane lining. Here are a few reasons why:1. Durable and Long-LastingPolyurethane lining is an incredibly durable material that can withstand extreme temperatures, chemicals, and abrasion. It is a highly resilient material that can last for many years, providing a low-maintenance solution to pipe repair and maintenance.2. Resistant to Corrosion and RustSteel pipes are often susceptible to corrosion and rust, which can lead to pipe failure and contamination. Polyurethane lining provides an impermeable barrier between the steel pipe and the environment, preventing rust and corrosion from occurring.3. Non-Toxic and SafePolyurethane lining is a non-toxic material that is safe for use with drinking water and other applications where food and beverages are involved. It is also an environmentally friendly solution that can reduce the need for pipe replacement, ultimately reducing waste and saving resources.4. Easy InstallationPolyurethane lining can be easily applied to steel pipes through a variety of methods, including spray-on, dipping, or rolling. This makes it a quick and cost-effective solution for pipeline repair and maintenance.Overall, polyurethane lined steel pipe offers a range of benefits that make it a superior choice for pipeline maintenance and repair. At Vulcan Painters, our expertise in pipe lining and coating, combined with our commitment to quality and service, ensure that our clients receive the best possible solutions for their pipeline needs.Keywords: Pipe Lining, Pipe Coating, Polyurethane Lining, Steel Pipe, Ductile Iron Pipe, Infrastructure Repair, Maintenance, Rust, Corrosion, Non-Toxic, Safe, Environmentally Friendly, Easy Installation, Vulcan Painters.
Versatile Metal Conveyor Belts for Diverse Applications
and Product Range.Metal Conveyor Belts: The Ultimate Solution for Every ApplicationConveyor belts are an essential component of industrial processes. They play a critical role in the transportation of materials, products, and goods across various stages of production and distribution. While there are different types of conveyor belts available in the market, metal conveyor belts are one of the most popular choices. They offer numerous advantages, such as strength, durability, and versatility, making them the ultimate solution for every application.At (need to remove brand name), we offer a wide range of metal conveyor belts that cater to various industries and applications. Our product range includes stainless steel belts, wire mesh belts, flat wire belts, chain belts, and modular belts, among others. Each of these belts features unique characteristics that make them suitable for specific purposes. Let's delve into each of them and see how they can benefit your business.Stainless Steel BeltsStainless steel belts are the most widely used metal belts in food, chemical, and pharmaceutical industries. They are highly resistant to corrosion, heat, and wear, making them ideal for conveying materials that require strict hygienic standards and harsh operating conditions. Stainless steel belts come in different grades, such as 304, 316, and 316L, to suit different environments and applications.Wire Mesh BeltsWire mesh belts consist of interlocked chains and metal wires that form a flat surface. They provide excellent airflow and drainage, making them perfect for applications such as drying, cooling, and heat treatment. Wire mesh belts are also highly durable, withstanding extreme temperatures and heavy loads.Flat Wire BeltsFlat wire belts are similar to wire mesh belts but consist of flat wires instead of interlocked chains. They offer smoother carrying surfaces, making them suitable for conveying delicate materials such as electronics and textiles. Flat wire belts also provide excellent heat and corrosion resistance, making them ideal for high-temperature and harsh environments.Chain BeltsChain belts are comprised of metal links that form a continuous loop. They are ideal for heavy-duty applications that require high strength and load-carrying capacity, such as mining, construction, and automotive industries. Chain belts can also withstand extreme temperatures, making them ideal for extreme heat or cold conditions.Modular BeltsModular belts are made of plastic or metal modules that interlock to form a continuous surface. They are ideal for applications that require precision, such as packaging, and can handle both light and heavy materials. Modular belts also come in different colors, making them suitable for color-coded sorting and identification.Overall, metal conveyor belts offer numerous benefits and are suitable for various applications. At (need to remove brand name), we provide a wide range of metal conveyor belts to cater to different industries and applications. Our belts are highly durable, reliable, and customizable to fit your exact needs. Contact us today to learn more about our products and how we can help improve your industrial processes.
Expert Tips for Conveyor Belt Splicing Techniques: Best Methods Revealed
Tips and Procedures for Splicing Conveyor Belts: Why Hot Vulcanization is RecommendedConveyor belts play a critical role in the transportation of varying products in different manufacturing and industrial settings. With the constant use of conveyor belts, it's inevitable that they will eventually wear and tear, break, and require repair. In such moments, conveyor belt splicing is essential.Several methods can be used to splice conveyor belts, including mechanical splicing and hot vulcanization. However, when it comes to choosing the best option, experts recommend hot vulcanization. This method involves the use of heat and pressure to bond the repair material to the damaged area, making it a durable, strong, and long-lasting solution.Why Choose Hot Vulcanization?Although hot vulcanization is more expensive and takes longer than mechanical splicing, it offers numerous benefits. Some of these benefits include:1. High Quality and Long-Lasting RepairsHot vulcanization enables you to achieve high-quality, long-lasting conveyor belt splicing solutions. The vulcanized splice is strong, durable, and often outlasts the original belt. The method ensures that you don't have to worry about conveyor downtime due to belt failure.2. Improved SafetyImproved safety is a significant benefit of vulcanized conveyor splicing. The process helps ensure that the conveyor belt is strong and direct to avoid accidents in the workplace. A damaged conveyor belt can result in injury or accidents that can cause significant damage to personnel, facilities, machinery, and products.3. Increased Conveyor EfficiencyVulcanized conveyor belt splicing helps optimize conveyor efficiency by minimizing downtime and reducing maintenance costs. This implies that you can focus more on production and less on conveyor maintenance, repair, and replacement.Procedures for Hot Vulcanization of Conveyor BeltsVulcanizing a conveyor belt involves several steps, including preparation, curing, and finishing. Here is a step-by-step guide to hot vulcanizing conveyor belts:1. Preparationa) Clean the damaged area by removing any dirt or debris.b) Mark the damaged section of the belt using a chalk or marker.c) Cut along the marked section using a repair strip cutter.d) Trim the end of the cut to make the repair strip neat.e) Buff both the belt and repair strip with a grinder to create a smooth surface.2. Curinga) Lay the belt ends together on a curing table and ensure that the splices are square.b) Apply hot vulcanizing material to both the belt ends.c) Use a putty knife to spread the material evenly.d) Position the repair strip and ensure that it covers the entire damaged area.e) Cover the repair strip with a release cloth.f) Use a vulcanizer to heat the splice to cure the hot vulcanizing material.3. Finishinga) Remove the release cloth.b) Cut any excess material from around the splice.c) By using a pry bar, carefully remove the splicing frame.d) Finally, inspect the conveyor belt to ensure the splice is cured correctly.In conclusion, conveyor belt splicing is a crucial process that should be taken seriously to ensure that the conveyor system operates smoothly and efficiently. Although there are several different belt splicing methods, hot vulcanization is the most reliable and durable solution. Following the proper hot vulcanization procedures will guarantee a high-quality repair that will last for an extended period.
Mechanical Devices for Material Movement: A Guide to Conveyors
Live Roller Conveyors: Streamlining Industrial Material HandlingEfficient material handling is crucial for any industrial operation. That is why sophisticated conveyors play a significant role in large farms, warehousing, freight handling, and industrial applications. One such type of conveyor is the Live Roller Conveyor.Live Roller Conveyor is an automated conveyor system that provides mechanized movement of materials by using rollers mounted on a conveyor bed. These rollers transport goods by rotating, which in turn, moves the products along the conveyor bed.Benefits of Live Roller Conveyors1. Continuous MovementLive Roller Conveyor is a high-speed system that can transport materials continuously. This allows for an uninterrupted flow of goods, ensuring the efficient movement of materials from one location to another.2. High Load CapacityLive Roller Conveyors can handle high loads, making them ideal for heavy-duty applications in industries such as automotive, manufacturing, and distribution.3. VersatilityLive Roller Conveyors are ideal for conveying a wide variety of materials, including boxes, packages, totes, and pallets. They can accommodate irregularly shaped items and can be customized with various roller widths, lengths, and configurations to suit specific material handling needs.4. Increased EfficiencyBy automating the material handling process, Live Roller Conveyors reduce manual labor requirements, minimizing errors, and saving valuable time. This translates to increased productivity and cost savings.5. Minimal MaintenanceLive Roller Conveyors have a simple design, making them easy to maintain, and require minimal upkeep. Their robust construction ensures durability and longevity even in the harshest industrial environments.6. SafetyLive Roller Conveyors comply with strict safety standards, making them a safe and reliable material handling solution. They are designed with features such as emergency stop buttons, safety guarding, and automatic shutoffs to prevent accidents.Applications of Live Roller ConveyorsLive Roller Conveyors are used in several industrial applications, including:1. Distribution CentersLive Roller Conveyors are ideal for the efficient movement of goods in distribution centers, including sorting, accumulating, merging, and diverting packages and parcels.2. ManufacturingLive Roller Conveyors transport raw materials and finished products on the factory floor, including heavy-duty assemblies, automotive components, and steel parts.3. WarehousingLive Roller Conveyors move products in and out of warehouses, minimizing manual labor and increasing efficiency.4. Food IndustryLive Roller Conveyors transport food and beverage products, including canned goods, bottles, and packaged food items, in a hygienic, safe, and efficient manner.In conclusion, Live Roller Conveyors are a smart investment for any industrial operation that emphasizes efficiency, safety, and cost savings. They streamline material handling, increase productivity, and reduce manual labor requirements. Whoever looking for high-performance material handling solutions should consider the benefits of a Live Roller Conveyor.
22mm to 15mm Rubber Water Hose for Flexible M Tube - Buy 10-Foot Extended CPAP BIPAP Tubing Hose with Free Shipping
to 15mm, CPAP, BIPAP, flexible tubing, braided hose, and M10*F1/2.As we all know, CPAP (Continuous Positive Airway Pressure) and BIPAP (Bilevel Positive Airway Pressure) are two effective treatments for sleep apnea. These medical devices deliver air pressure to keep airways open during sleep and improve breathing. However, to achieve the best results, it is essential to select the right tubing and hoses.If you are looking for a reliable and high-quality hose for your CPAP or BIPAP device, then the 10 Foot 22mm Extended CPAP BIPAP Flexible Air Tubing Hose Tube can be an excellent choice. This product is specially designed to provide maximum flexibility and comfort, making it easier to move around while using your CPAP or BIPAP.The hose is made of durable rubber material, which is both resistant to wear and tear and lightweight. The 22mm to 15mm conversion fitting provides a more secure and flexible connection between the hose and the device, reducing the risk of leaks and disconnections during use.Furthermore, the hose features a braided flexible design, which helps to prevent kinks and twists that can cause air supply disruptions. This design also provides an added layer of protection against punctures and damages that can occur when the hose comes into contact with sharp objects.The M10*F1/2 braided flexible hoses offer exceptional durability and longevity, reducing the need for frequent replacements. The hoses are also easy to install, requiring minimal effort and time. The braided hose ensures optimal airflow, which is crucial for the effectiveness of CPAP and BIPAP treatments.In conclusion, the 10 Foot 22mm Extended CPAP BIPAP Flexible Air Tubing Hose Tube is an excellent choice for anyone looking to enhance their CPAP or BIPAP treatment experience. With its flexible and durable design, you can rest assured of optimal air delivery, comfort, and reliability throughout your therapy.So, if you are looking for a high-quality hose for your CPAP or BIPAP device, it is time to try the 10 Foot 22mm Extended CPAP BIPAP Flexible Air Tubing Hose Tube. Enjoy the freedom of movement, comfort, and flexibility during sleep, and improve your overall breathing and sleep quality.
Types of Filter Presses: Understanding Cloth Filter Technology
: The Complete GuideFilter presses are widely used in various industries for solid-liquid separation. They are an important piece of equipment for many manufacturing processes that require efficient and effective filtration of liquid substances. The filter press has been around for over a century and has gone through several modifications, making it one of the most versatile and reliable filtration devices available today.A filter press is a batch-operated filtration system that separates solids from liquids using pressure filtration. It consists of a series of plate and frame filters that are lined with filter cloths. The liquid to be filtered is pumped into the press and forced under pressure through the filter cloth. The solid particles are retained on the cloth and form a filter cake, while the filtered liquid passes through the cloth and is collected in a pan or tank at the bottom of the press.Filter presses come in different sizes and designs, depending on the specific application and the type of material being filtered. The plate-and-frame filter press is the most common type of filter press and is the simplest in terms of operation and maintenance. It consists of a series of rectangular plates that are stacked together and connected with flexible hoses. Each plate is covered with a filter cloth that serves as the filtration medium.The cloth used for the filter press is an essential component of the filtration process. The quality of the cloth determines the efficiency and longevity of the filtration system. The filter cloth should be able to retain the solid particles while allowing the liquid to pass through it easily. It should also be able to withstand the pressure and temperature of the process.Filter press cloths come in different materials, such as polyester, polypropylene, and nylon. Polyester is the most commonly used material for filter cloths because of its versatility, strength, and resistance to abrasion and chemicals. Polypropylene is also a popular choice because of its resistance to acid and alkali. Nylon is used for filtration processes that require high-temperature resistance.When choosing a filter press cloth, it is essential to consider the type of material being filtered, the size and design of the filter press, and the operating conditions of the filtration process. The filter cloth should be selected based on its pore size, permeability, fabric strength, filtration rate, and cake release properties.In conclusion, filter presses are an essential piece of equipment for solid-liquid separation in various industries. The filter press cloth is a critical component of the filtration process and should be chosen based on the specific application and operating conditions. A high-quality filter cloth will ensure optimal filtration efficiency and longevity of the filtration system, resulting in better product quality and cost savings.
Flexible and Waterproof Expansion Joints for Asphalt Construction
and Expansion Joint Filler.Asphalt expansion joints are an essential component of road construction. They act as a buffer between different sections of the road, allowing for the natural expansion and contraction that occurs due to temperature changes. Without expansion joints, roads would have a tendency to buckle and crack, leading to costly repairs and safety hazards. In this blog post, we will explore the benefits of using asphalt expansion joints and why the use of an expansion joint filler is crucial.As mentioned earlier, asphalt expansion joints are necessary for the proper functioning of any road. They allow for the natural expansion and contraction of the road surface, which prevents it from cracking and becoming uneven. Expansion joints also play a vital role in managing water run-off. They keep water from seeping into the ground and causing damage to the road's substructure. As such, it's important to choose an expansion joint material that is durable, weather-resistant, and long-lasting.One of the most popular expansion joint fillers used in the construction industry today is the Asphalt Expansion Joint. Its composition of blended asphalts and mineral fillers make it waterproof, flexible, permanent, and self-sealing. These properties make it an excellent option for use in a variety of road construction projects.The Asphalt Expansion Joint is designed to withstand a range of temperature changes without losing its efficacy. The heat and pressure applied during its creation ensure that it remains pliable in both hot and cold weather. This ability to withstand temperature changes makes it a natural choice for use in climates that experience extreme weather conditions.Another major advantage of this expansion joint material is its ability to self-seal. This means that if there is any damage to the joint, it will automatically seal itself, preventing water from entering the road's substructure and causing damage. This option is particularly useful in areas where repairs are not easily accessible. The self-sealing nature of the Asphalt Expansion Joint ensures that roads remain safe and secure for an extended period.ConclusionAsphalt Expansion Joints are an indispensable part of any road construction project. They ensure the safety, durability, and longevity of roads by preventing cracking, buckling, and unevenness. The Asphalt Expansion Joint, in particular, is an excellent choice for expansion joint filler due to its versatile composition, making it waterproof, flexible, permanent, and self-sealing. This unique blend of properties makes it an excellent option for use in a variety of highway construction projects. By selecting the right expansion joint material, construction companies can build safer, longer-lasting roads that can withstand the test of time and extreme weather conditions.
Rubber Air Hose with 1/4-Inch MPT Ends and Bend Restrictors Offers High Performance for Air Tools
Telescoping Flanged Fittings for Simplified Retrofitting Applications
Dismantling Joint for HDPE Pipe – The Solution for Retrofitting ApplicationsA flanged pipe system is an essential component of a fluid transfer system. However, in retrofitting applications, adding, repairing or replacing flanged fittings can be a challenging task. Traditional methods require cutting of the flange, removal of bolts, and breaking the joint to take out the damaged fittings. This approach involves high cost, labor, and downtime. To overcome this challenge, engineers have developed a solution in the form of Dismantling Joint for HDPE Pipe.A Dismantling Joint for HDPE Pipe is a special type of joint that allows the disassembly and reassembly of flanged pipe systems without cutting or breaking the pipe. It is suitable for retrofitting applications where the replacement of flanged fittings is necessary. The joint consists of two halves that can be separated without disrupting the pipeline's flow. The halves are held together by bolts, nuts, and a sealing gasket that ensures tightness and prevents leaks.The joint provides several advantages over traditional methods. With the Dismantling Joint, the installation and replacement of flanged fittings become more manageable, less time-consuming, and more cost-effective. Unlike traditional methods that require cutting of the flange, the joint eliminates the need for cutting and welding of the pipe, resulting in less downtime and disruption. Additionally, the joint's modular design allows for fast and easy assembly and disassembly, reducing labor costs.Another important advantage of the Dismantling Joint is its superior performance. The joint has a telescopic design that allows for flexibility in movement, expansion, and contraction of the pipeline. This feature makes it suitable for applications that involve temperature variations or ground movement. The joint's flexibility ensures that the system remains stable and permanent, preventing leaks and minimizing the risk of failure.The Dismantling Joint also provides versatility in its application. It can be used for various pipe materials, including HDPE, PVC, and cast iron, making it a go-to solution for retrofitting applications. The joint is also compatible with various flange standards, including ANSI, DIN, BS, and JIS, providing a solution for a wide range of piping systems.In conclusion, retrofitting applications involving flanged pipe systems require a solution that is easy to install, cost-effective, and reliable. The Dismantling Joint for HDPE Pipe provides the solution for adding, repairing, or replacing flanged fittings within a flanged pipe system. Its modular design, flexibility, and compatibility make it a versatile solution suitable for the majority of retrofitting applications.Therefore, if you are looking for a solution for your retrofitting application, consider the Dismantling Joint for HDPE Pipe. It reduces downtime, labor costs, and ensures long-term stability and reliability of your piping system. Remember, seamless fluid transfer depends on the quality of your piping system, and the Dismantling Joint for HDPE Pipe is one step closer towards achieving that goal.
Pipe Lining and Coating: Why Polyurethane Lined Steel Pipe is the Way to GoPipe lining and coating have become increasingly important in the realm of infrastructure repair and maintenance. With aging pipelines and increased demand for water and waste water treatment, it is crucial to protect and revamp these systems to prevent environmental damage, contamination, and loss of valuable resources.At Vulcan Painters, we specialize in coating ductile iron pipe, steel pipe, and structural steel, as well as tanks and water and waste water equipment at sewage treatment facilities. Our expertise in pipe lining and coating has allowed us to become a trusted name in the industry, providing high-quality services that ensure the longevity and safety of pipelines.One type of pipe lining that we highly recommend for steel pipelines is polyurethane lining. Here are a few reasons why:1. Durable and Long-LastingPolyurethane lining is an incredibly durable material that can withstand extreme temperatures, chemicals, and abrasion. It is a highly resilient material that can last for many years, providing a low-maintenance solution to pipe repair and maintenance.2. Resistant to Corrosion and RustSteel pipes are often susceptible to corrosion and rust, which can lead to pipe failure and contamination. Polyurethane lining provides an impermeable barrier between the steel pipe and the environment, preventing rust and corrosion from occurring.3. Non-Toxic and SafePolyurethane lining is a non-toxic material that is safe for use with drinking water and other applications where food and beverages are involved. It is also an environmentally friendly solution that can reduce the need for pipe replacement, ultimately reducing waste and saving resources.4. Easy InstallationPolyurethane lining can be easily applied to steel pipes through a variety of methods, including spray-on, dipping, or rolling. This makes it a quick and cost-effective solution for pipeline repair and maintenance.Overall, polyurethane lined steel pipe offers a range of benefits that make it a superior choice for pipeline maintenance and repair. At Vulcan Painters, our expertise in pipe lining and coating, combined with our commitment to quality and service, ensure that our clients receive the best possible solutions for their pipeline needs.Keywords: Pipe Lining, Pipe Coating, Polyurethane Lining, Steel Pipe, Ductile Iron Pipe, Infrastructure Repair, Maintenance, Rust, Corrosion, Non-Toxic, Safe, Environmentally Friendly, Easy Installation, Vulcan Painters.